Unitized Cavity Wall Design and Implementation
Practical Case Studies
Presented on October 10, 2024 at Facade Tectonics 2024 World Congress
Sign in and Register
Create an Account
Overview
Abstract
Double Skin Facades (DSF), constructed from individual aluminum framed curtain wall assemblies, provide a means of achieving acoustic and thermal performance that exceeds what can be produced by single leaf systems. To harness these benefits additional considerations are required throughout the processes of design, fabrication, site logistics, installation, and envelope commissioning. An extensive conceptual discussion of these topics is provided. Furthermore, two example problems are investigated. In the first example problem, the results of a computational fluid dynamics (CFD) model in two configurations are compared with a model of effective thermal conductivity derived from the experimental work of El Sherbiny (1982). In the first configuration the CFD model incudes turbulence modeling by the two-equation method of Mentor (1994) and in the second, no turbulence was modeled. It was found that the results of both cases compared favorably when values of the effective conductivity predicted were compared to the experimental work; however, significant variations in temperature determined by the CFD analysis cannot be replicated by applying the effective conductivity determined to a model of diffusive heat transfer. The implications of this outcome for cavity wall design are discussed. In the second example problem WINDOW FEA software is used to analyze temperature distributions in sealed double facade cavities with and without blinds. It is shown that the placement of insulated glass in either the inner or outer leaf, and shade deployment, significantly affect cavity temperatures which range from 101 F to 176 F.
Authors
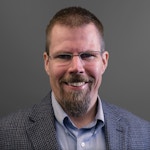
Dan Bettenhausen, Ph.D.
Director of Mechanical Engineering
Enclos
dbettenhausen@enclos.com
Keywords
Paper content
Nomenclature
T Temperature
t Time
xi Spatial Coordinate i
ρ Mass Density
Ui Fluid Velocity Along Coordinate i
p* Modified Pressure
μ Dynamic Viscosity
μt Turbulent Viscosity
gi