Tool For Facade Inspection Traceability
Simple Method to Report Building Envelope Defects
Presented on October 10, 2024 at Facade Tectonics 2024 World Congress
Sign in and Register
Create an Account
Overview
Abstract
Building façade inspections have multiple objectives, such as forensic investigation of a failure, maintenance code compliance, etc. Architects, Engineers, and technicians doing façade inspections must gather all the technical information needed to be used by others. General contractors, building managers, lawyers, and other forensic investigators use this information obtained during the façade inspections. The results of the façade inspections must be clear, objective and traceable.
Traceable information requires that every deficiency/defect receives a unique identification that allows other professionals to follow its evolution since the day it was discovered/reported, up to the day when it is addressed. The data management aspects of traceability identify and reference the necessary requirements for capturing and sharing data using a simple model.
This simple model has been developed. This method can be used to report and trace all the deficiencies discovered during façade inspections. This method is based on the use of databases that allow for the identification of every deficiency and links all the information that must be prepared for others. The deficiencies are recorded according to the severity of the defect and the time required to be resolved. The simplicity of the software’s interface accelerates the data entry and the management of the information. The database software responds to these questions: What (what is the deficiency?), Where (where is it precisely located in the facade?), When (required time for repair?), and Who (who is responsible for the defect and/or repair?).
Authors
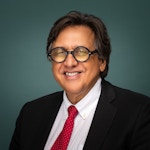
John Medina
Owner, Senior Principal
jmedina@miamicurtainwall.com
Jorge Moya
Forensic and Chemical Analyst
jmoya@miamicurtainwall.com
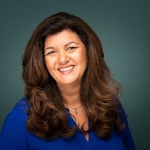
Maria Moral
Architect - Junio Principal
mmoral@miamicurtainwall.com
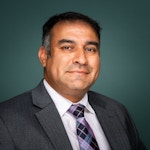
Guillermo Saavedra
Architect - Junior Principal
gsaavedra@miamicurtainwall.com
Keywords
Paper content
TOOL FOR FACADE INSPECTION TRACEABILITY
Building inspection and condition assessments have been deemed as an essential measure to preserve the functionality and integrity of buildings. The exposure of façades experiencing