Sustainable Materials
The Good, the Bad, and the Dangerous of Welding Stainless Steel
Sign in and Register
Create an Account
Overview
Abstract
Stainless steel has been successfully used in building envelopes since the completion of the Chrysler building in 1928. Today, it is used as both a structural material and for skin components. Its corrosion resistant properties give it a long service life, and it requires very little maintenance, making it an ideal material choice in harsh environments. The end of life recyclability is another desirable quality in-today’s buildings. The development of new stainless steel alloys has broadened the design team’s material palette. These higher strength alloys allow components to be designed smaller and from a material that will last forever in almost any condition.
In many cases, the design team’s desire to use state of the art materials has outpaced the experience set of fabricators. As designers and fabricators work together on innovative building components, one area of critical interest is the welding of stainless steels. High performance stainless steels require specialized welding knowledge and more complex, labor-intensive procedures. For example, the long life and aesthetic advantages of commonly used stainless steels can be jeopardized if they are exposed to improper heating and cooling during the welding process. In some cases, the improper welding of high-performance alloys can lead to a severe decrease in corrosion resistance or an increased risk of structural failure.
This paper provides an overview of best practices for common alloys that are covered by AWS D1.6 and a more detailed examination of how design practitioners can ensure that high-performance alloys are treated properly in fabrication. The content will not be overly technical, but it will provide a working knowledge of what is achievable without special testing and an understanding of the development of one-off welding procedures and the qualification of welders for unique materials. A better understanding of the welding metallurgy and behaviors of high-performance alloys will provide designers with the necessary tools for assessing the cost-benefit and inherent risks in these procedures. Designers will learn more about avoiding problems that are expensive to remediate and potentially dangerous. Specific examples of built work will be used to show how these challenges were overcome during the course of design and fabrication.
Authors
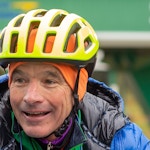
Michael C. Mulhern P.E.
President
TriPyramid Structures
mcm@tripyramid.com
Introduction
As the use of stainless steel in buildings increases, there is an increase in the number and types of stainless steel alloys that designers would like to use. There are
Access Restricted
Section 1: A brief introduction to the types of stainless steel
Stainless steel is a ferrous metal. It is generally defined as having greater than 11% chromium (Cobb, 2010). Like all ferrous metals, it cools into several types of micro structure
Access Restricted
Section 2: Welding Standards for Stainless Steels
In the United States, most of the codes and standards groups use the standards developed by the American Welding Society (AWS) as the applicable guide for welding procedures and weld
Access Restricted
Section 3: Welding considerations by SS type
Austenitic Stainless Steels
By far the most common stainless steels are T304/304L and T316/316L. There are AWS prequalified welds for a vast majority of the welds used in structural applications. However
Access Restricted
Section 4: General Considerations in All Stainless Steel Welding
The inclusion of stainless steel in building projects is generally driven by either a desire for long life in difficult environmental conditions or aesthetic concerns. It is important to understand
Access Restricted
Conclusion
Each of the three types of stainless steel commonly used in structural applications can be successfully welded. Annealed Austentic stainless steel alloys are the easiest to specify since there are
Access Restricted
Rights and Permissions
REFERENCES
Cobb, Harold. The History of Stainless Steel. ASM International, 2010.
Outokumpu. “Handbook of Stainless Steel.” [HSS], 2013.
Bhadeshia, H.K. “Interpretation of the Microstructure of Steels.” University of Cambridge, 2008.
Outokumpu. “The Outokumpu Corrosion Handbook” [OCH], 2010.
Houska, Catherine. “Stainless Steels in Architecture, Building and Construction: Guidelines for corrosion protection.” Nickel Institute Reference Book Series No 11.024, 2014.
Mulhern, M. “Stainless Steel 101: High Performance Alloys for Architecture”, FTI, 2018 World Congress
AWS. “Structural Welding Code – Stainless Steel.” AWS D1.6/D1.6M:2007
Sowa,R., S. Arabasz, E. Roga, A. Dziedzic, I. Dul, A. Kowal, M. Parlinska-Wojtan. “Influence of Double Solution Treatment on Hardness in 17-4PH Steel” Journal of Engineering & Processing Management, Vol 7, No. 1, 2015.
Bhaduri, A.K, S. Sujith, G.Srinivasan, T.P.S. Gill, S.L. Mann. “Optimized Postweld Heat Treatment Procedures for 17-4PH Stainless Steels.” Welding Research Supplement, 1995.
BSSA. “Stress relieving heat treatments for austenitic stainless steels.” [AST] http://www.bssa.org.uk/topics.php?article=76 / (accessed 9/30/2017)
Armco Steel. “17-4PH Product Data Bulletin.” BS-82. 1986
NiDI. “High-Temperature Characteristics of Stainless Steels.” Designers’ Handbook Series No. 9004
BSSA. “Duplex Stainless Steels- A Simplified Guide.” [DSG] http://www.bssa.org.uk/topics.... / (accessed 9/30/2017)
IMOA. “Practical Guidelines for fabrication of Duplex Stainless Steels.” International Molybdenum Association, 2009.