The Scope of the Structural Glass Design Manual
A voluntary specification and design guide - contents.
Presented on October 10, 2024 at Facade Tectonics 2024 World Congress
Sign in and Register
Create an Account
Overview
Abstract
The technology of glass now allows glass to be fabricated in sizes and structural configurations not previously conceivable. The standards and codes have not kept up. Achieving a comprehensive consensus standard is difficult, so voluntary specifications serve a useful purpose as we move forward with using glass as a structural material. This paper is a critical look at current standards, some common myths about glass design and provides a framework to design confidently and safely with structural glass. At the time of the conference it is anticipated that the Structural Glass Design Manual will be available in final public format for comment.
Authors
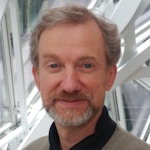
Richard Green SE PE P.Eng CPEng
Principal / Owner
Green Facades LLC
richard@greenfacadesllc.com
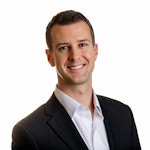
Andrew Crosby P.Eng LEED® AP BD+C
Principal
Read Jones Christoffersen Ltd.
acrosby@rjc.ca
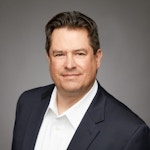
Terrence McDonnell SE SECB PE P.Eng
Principal
Klein & Hoffman
trmcdonnell@kleinandhoffman.com
Keywords
Paper content
The United States, along with much of the world, lacks standardized practices for utilizing glass as a structural material in buildings. Over the past decade, several challenges have
Access Restricted
Rights and Permissions
ANSI/AISC 360 Specification for Structural Steel Buildings. American Institute of Steel Construction
ASTM E1300–- Standard Practice for Determining Load Resistance of Glass in Buildings, ASTM International. West Conshohocken, PA
ASTM E2751 - Standard Practice for Design and Performance of Supported Laminated Glass Walkways, ASTM International. West Conshohocken, PA
Australian Standard AS1288 Glass in Buildings – Selection and Installation, Standards Australia GPO Box 476 Sydney, NSW 2001 Australia.
Bedon, Chiara, Belis, Jan, and Amadio, Claudio (2015). Structural assessment and lateral-torsional buckling design of glass beams restrained by continuous sealant joints. Engineering Structures, 102 (11): 214-229.
Bedon, Chiara (2021). Lateral-torsional buckling (LTB) method for the design of glass fins with continuous lateral restraints at the tensioned edge. Composite Structures, 266: 113790.
CEN/TS 19100-1 Design of glass structures–- Part 1: Basis of design and materials
D’Ambrosio, Gianmaria, and Galuppi, Laura (2020). Enhanced effective thickness model for buckling of LG beams with different boundary conditions. Glass Structures & Engineering, 5(2): 205-210.
EN 16612: Glass in building. Determination of the lateral load resistance of glass panes by calculation
EN 1993-1-1: Eurocode 3: Design of steel structures–- Part 1-1: General rules and rules for buildings
Galuppi, Laura, and Royer-Carfagni, Gianni (2014). Enhanced Effective Thickness of multi-layered laminated glass, Composites: Part B, 64: 202–213.
Galuppi, Laura, and Royer-Carfagni, Gianni (2020). Enhanced Effective Thickness for laminated glass beams and plates under torsion. Engineering Structures, 206: 110077.
Galuppi, Laura, Manara, Giampiero, and Royer-Carfagni, Gianni (2013). Practical expressions for the design of laminated glass. Composites: Part B, 45: 1677–1688.
Green, R., Bedon, C., Galuppi, L.: Design and stability of laminated glass fins with continuous lateral silicone restraint. Glass Structures and Engineering 8(3):1-20 http://dx.doi.org/10.1007/s40940-023-00224-1
Green, R., Bedon, C., Galuppi, L.: Moment capacity of imperfect slender beams and cantilevers with continuous silicone restraint, Challenging Glass Conference 9 (CGC9), 2024.
Griffith, A.A.: The Phenomena of Rupture and Flow in Solids. Phil. Trans. R. Soc. A221, 163-163 (1920)
Haldimann, M; Luible, A; Overend, M - Structural Use of Glass IABSE (2008)
Kala, Zdeněk (2013). Elastic Lateral-Torsional Buckling of Simply Supported Hot-Rolled Steel I-Beams with Random Imperfections. Procedia Engineering 57: 504-514.
NCCI SN-003-EN-EU NCCI: Elastic critical moment for lateral torsional buckling, by Access Steel. https://eurocodes.jrc.ec.europa.eu/doc/WS2008/SN003a-EN-EU.pdf
NCCI SN-006-EN-EU NCCI: Elastic critical moment of Cantilevers, by Access Steel.
Nizich, Adam J, La GReca, Andrea M and Galuppi, Laura. Advances in Effective Thickness For Laminated Glass Structural Design, Facade Tectonics Institute's biennial World Congress, 2022.
Simulia (2022), ABAQUS computer software, v.6.14, Providence, RI, USA.
Strand7 finite element software, R3.1.1, Sydney, NSW, Australia. https://www.strand7.com/