SSG and Seismic
Design Boundaries in Advanced Modeling
Presented on October 13, 2022 at Facade Tectonics 2022 World Congress
Sign in and Register
Create an Account
Overview
Abstract
With the advent of more sophisticated analysis methods and the desire to optimize geometries of structural silicone joints in high performance designs with extreme loading events like seismic, there is a continual need to provide better material behavior models and durability predictions for structural silicone glazing. Seismic applications incorporate repetitive loading cycles that can highlight the stress relaxation behavior of silicone elastomers.
Previous work from the authors have combined Finite Element Models and experimental validation to determine potential failure models as a function of time. Potential critical model outputs that may be useful for design boundary conditions were observed that extend beyond current design practices. These outputs were validated against the performance of physical mock-ups tested to the simulated models.
Authors
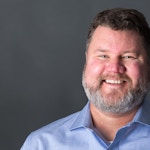
Jon Kimberlain
Senior Scientist
Dow
jon.kimberlain@dow.com
Valerie Hayez
Senior Scientist
Dow
valerie.hayez@dow.com
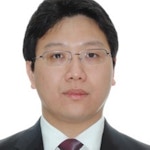
Jie Feng
Research Scientist
Jfeng2@dow.com
Mark Mirgon
R&D Technologist
mhmirgon@dow.com
Keywords
Introduction
Some of the world’s largest metropolitan areas — including Tokyo, Jakarta, Shanghai, and Los Angeles — are all located within highly active seismic regions. Earthquakes signify one of the greatest damaging natural hazards worldwide and these high risk, low likelihood, incidents lead to major architectural and human impact especially as population density of urban centers continues to increase. Glass facades are amongst the most popular building envelope systems in contemporary architecture. The effects of seismic action on curtain wall façades are transmitted through the structure on which they are attached to. The more inflexible the exterior materials for the walls and cladding of a building, the more potential damage there is likely to be during a seismic event. Damage includes serviceability failures, such as gasket dislodging, sealant damage, glass edge damage and glass cracking which require building envelope repairs but can also lead to more serious failures such as falling glass. The damage to the glazing typically results from incompatibility between the deformation characteristics of the structural framing and the movement capability of the cladding, e.g. insufficient perimeter joint widths and lack of slip accommodating connections [1]. Tying into the stable foundation characteristic, structural and nonstructural components should therefore ideally be interconnected so inertial forces can dissipate.
To evaluate seismic performance of dry glazed and bonded curtain wall systems, experimental full scale tests [1, 2, 3, 4, 5, 6] are typically used according to various seismic codes. One such code is the American Architectural Manufacturers Association (AAMA) 501.6 testing standard [7], which is characterized by monotonically increasing-amplitude sinusoidal drift cycles that determine the serviceability and ultimate drift limits for architectural glass components subjected to cyclic, in-plane racking displacements. Silicone bonded curtain wall systems are a durable proven façade assembly system which can also contribute to a better seismic resistance of the building and façade. Since the glass units are not captured in a rigid metal frame, the possibility for glass breakage due to contacting metal is reduced. Based on the results obtained in [3, 4, 5, 6] and comparisons with data collected on dry-glazed curtain walls, it appears that the serviceability and ultimate drift capacities of silicone structurally glazed (SSG) systems are higher than their dry-glazed counterparts.
Full scale testing can be time consuming and typically does not allow evaluation of all desired system variations due to cost of samples. But these experimental results prove valuable to build and validate theoretical models, using tools such as Finite Element analysis (FEA). FEA has been used successfully to predict the stresses and strains of glazing systems under various loading conditions [8, 9]. Once the modeling has been validated through experimental testing and is able to predict these results, the model can be considered for parametric studies as an alternative to experimental testing. The use of FEA has increased recently to evaluate different system options in mechanically fixed façades or unitized façades exposed to seismic loading. The developed FE models for stick systems under in-plane racking [10, 11, 12, 13, 14] investigated aspects such as the interaction between glass panels and aluminum frame, the gasket friction and the glazing-frame connection stiffness. The results of the models predict with reasonable accuracy the experimental test results. Additional work is still needed to refine the model by adding variables such as insulating glazing or laminated glass to the model. The research presented in [12] focusses on stick wall systems, this time including IGU and laminated glass. In [14], the experimental testing of a unitized façade was used to develop a FEM model with the software Straus7 [15] to describe the interaction between glass plate and unit frame. The rotational and deformational behavior of the façade during all the applied horizontal displacements, in and out-of-plane oriented, was correctly modelled. The stress distribution results showed a different behavior depending on the direction of the applied displacement. The model was found to describe an idealized behavior of the façade, as friction was not modelled. Including friction is expected to increase the stress values. Further differences between experimental and model results were attributed to the elastic numerical definition, in terms of stiffness values, of the springs defining the silicon joint. More recently, [16] has used full scale experimental data to develop and calibrate FEM procedures for four-sided structural sealant glazing curtain wall systems with reentrant corners. The research was mainly concentrated on the selection of element types and appropriate material inputs to develop a simplified FE model using SAP2000 [17], accessible to a wider range of users and less time consuming when running. The goal of the model was to allow the evaluation of the translations and rotations of the glass relative to the frame and to predict glass-to-glass contact. However, attention was also dedicated to numerically determining the critical stresses and strains leading to sealant failure. While volumetric elements are typically used for structural silicone modeling, shell-thick elements were used which combine membrane shear to represent the longitudinal shear and plate shear to represent the transverse shear which is the primary deformation in the AAMA 501.6. The shell element uses linear material behavior data. This and previous seismic experimental studies performed on four-sided SSG systems [5, 14] both indicate that linear elastic behavior would be a valid way to conservatively predict the sealant stresses and system behavior, up to allowable drift levels, before other more critical safety failures occur to the building. Hyperelastic behavior is however typical of the silicone elastomer when strained in tension. When the same sample is strained in the shear, the resulting stress-strain behavior more approximates a linear relationship when considering the modulus of shear, G. A linear model based on shear modulus was used in [16] for the finite element modeling under the assumption that the sealant under seismic testing would behave mostly in shear. The linear model and the selected boundary conditions eventually resulted in some significant difference between model prediction and experimental data, which indicates the need to refine the material model.
The following research reviews the difference between an actual four-sided structurally glazed curtain wall assembly tested to AAMA 501.6 and compared to a theoretical FEA model using more sophisticated hyperelastic material models for the structural silicone. The model used a highly discretized mesh in an effort to more accurately describe the sealant behavior. Model outputs were compared to regions where failure was observed in the physical testing to understand if parametric conclusions could be made. These outputs were calibrated initially using industry standards of material behavior performance as part of the evaluation process.
Material Model for Silicone Structure Sealant
The material behavior of DOWSIL™ 983 Structural Glazing Sealant, a typical silicone structural sealant, can be characterized by a fitted Hyperelastic material model, such as Mooney-Rivlin model (Table 1) [18]
Access Restricted
Development of Full Scale FEA Model for Seismic Test
With the sealant material model and strain-based design criteria calibrated from TA joint test, the seismic and drift performance of a window system bonded by SSG can be evaluated through
Access Restricted
Simulation of Structural Sealant Performance in a Seismic Drift Loading Test
The overall deformation for the window system is simulated with an in-plane seismic drift of 114.3mm, applied onto the aluminum frame. From simulation, it is found that an out of
Access Restricted
Test Results from Seismic Drift Test and Comparison to FEA Simulation
In addition to FEA based numerical simulation, full scale seismic drift test according to AAMA 501.6 was performed for the window system design in Figure 3 and Figure 4. Based
Access Restricted
Summary and Conclusions
This study explored the structural sealant joint performance modeling for seismic drift test through FEA simulation.
By calibrating the maximum principal strain limit for the sealant material from TA joint
Access Restricted
Rights and Permissions
- Bedon C. et al., Performance of structural glass façades under extreme loads – design methods, existing research, current issues and trends, Construction and Building Materials 163 (2018) 921-937
- Memari A.M, Behr R.A, Kremer P.A, Seismic Behavior of curtain walls containing insulating glass units, J. Archit. Eng., 9(2), 70-85 (2003)
- Zarghamee M.S., Schwartz T. A., Gladstone M., Seismic behavior of structural silicone glazing, Science and Technology of Building seals, sealants, glazing and waterproofing, 6th Volume, ASTM STP 1286, James C. Myers, ed., American Society for Testing and Materials, Philadelphia (1995)
- Memari A. et al, Seismic performance of Two side structural silicone glazing systems, journal of ASTM International, Vol 3, No. 10 (2006)
- Broker K.A., Fisher S., Memari A.M., Seismic Racking Test Evaluation of Silicone Used in a 4-Sided Structural Sealant Glazed Curtain Wall System, 4th Symposium on Durability of Building and Construction Sealants and Adhesives (2011)
- Memari A.M, Fisher S, Krumenacker C., Broker K.A, Modrich R.-U. , Evaluation of the Structural Sealant for Use in a Four-Sided Structural Sealant Glazing Curtain-Wall System for a Hospital Building, Journal of ASTM International, Vol. 9, No. 4 (2012)
- AAMA 501.6
- Kimberlain J., Carbary L.D., Descamps P., Hayez V., Feng J., Durability of Structural Silicone Sealant in Cold Bent Glazing Design, Proceedings of Glass Performance Days (2019)
- Sitte S., Hayez V., Kimberlain J., Mirgon M., Feng J., Structural silicone joint behaviour study for cold bent glass, Glass Struct. Eng. 6 (1): 1-25 (2021)
- Memari A.M., Shirazi A, Kremer P.A., Behr R.A, Development of Finite-element modeling approach for lateral load analysis of dry-glazed curtain walls, J. Archit. Eng., 17 (1):24-33 (2011)
- Simmons N. C., Analytical evaluation of racking performance of four-sided structural silicone glazing curtain wall systems, Thesis in Architectural Engineering, The Pennsylvania State University, The Graduate School, College of Engineering (2011)
- Caterino N., Del Zoppo M., Maddaloni G, Bonati A., Cavanna G., Occhiuzzi A., Seismic Assessment and finite element modelling of glazed curtain walls, Structural Engineering and Mechanics, Vol 61, N°1, 77-90 (2017)
- Aiello C., et al, Experimental and numerical investigation of cyclic response of a glass curtain wall for seismic performance assessment, Construction and Building Materials 187, 596-609 (2018)
- Galli U., Seismic Behaviour of curtain wall façades: a comparison between experimental mock-up test and finite element analysis, Master thesis, University of Milan, Italy (2011)
- Straus7, https://www.enginsoft.com/solu... A.M., Simmons N., Solnosky R.L., Developing FEM procedures for four-sided structural sealant glazing curtain wall systems with reentrant corners, Buildings, 11, 597 (2021)
- SAP2000, https://www.csiamerica.com/pro...
- DOWSIL™ 983 Structural Glazing Sealant Behavior Data Sheet
- Abaqus, https://www.3ds.com/products-s...
TM Trademark of the Dow Chemical Company ('Dow') or an affiliated company of Dow