Modeling Megapanels
Balancing Cost, Pattern, and Panelization
Presented on October 13, 2022 at Facade Tectonics 2022 World Congress
Sign in and Register
Create an Account
Overview
Abstract
Large format, steel-stud framed “megapanel” facades with rainscreen cladding create uniquely complicated requirements for digital documentation and 3D coordination. This can be further complicated by design requirements such as irregular rainscreen joints, non-repetitive rainscreen patterns, punched windows, balconies, and vents.
The two 13-storey towers of the mass-timber McEvoy & Dupont project have complex aesthetic requirements with a dual-theme rainscreen pattern, along with a requirement for off-site fabricated megapanels. The economics of the project require a close collaboration between SERA, the architect, and Lendlease, the Design Build partner, to optimize costs and constructability. A prefabricated megapanel approach streamlines on-site construction, but the architectural documentation required a non-traditional approach to communicate design intent, maintain cost, and meet technical requirements.
To do this, the architectural team created an iterative process for modelling the megapanels that could be adjusted throughout the design stages. This paper discusses this process of design, modeling, and documentation along with the coordination with the cost model that was required.
SERA defined cladding types in the Revit model and drawings, while Lendlease worked with potential subcontractors to get pricing feedback. Priority was placed on the resolution of the megapanels, with support from envelope consultant RDH. As the architectural team worked, Lendlease costed and considered constructability of options, providing feedback to the architectural team. Cost feedback was taken on board, and the model was adjusted to ensure that design and cost were working together.
In summary, large format megapanels can be an efficient and cost-effective solution that allows for factory fabrication to tight tolerances and rapid site installation. For the McEvoy project, their unique attributes required a novel, non-traditional means of architectural documentation and close collaboration between design, engineering, cost, and Design Build partners.
Authors
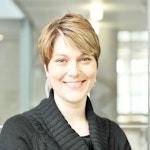
Elizabeth Bishop, AIA, LEED AP
Creative Design Director
elizabeth@workbenchbuilt.com
Emily Green, NCARB, LEED GA
Associate
emilyg@seradesign.com
Lisa Podesto, PE
Timber & Innovations Specialist
Lendlease
lisa.podesto@lendlease.com
Keywords
Introduction
The quest to design a versatile, high-quality, high-performance envelope system that achieves architectural goals while meeting an aggressive cost plan has driven experimentation with novel means of panelizing facades. The “megapanel” is typically a fabricated steel frame cladding panel with light-gauge stud framing infill, insulation, punched windows, and a rainscreen external skin. They are fabricated as complete units off site, with the intent of achieving high quality control on the panel production while significantly reducing the amount of on-site labor. Installation is rapid, with a “just-in-time” process of panels picked from arriving trucks by the tower crane and lifted into place on the structure as an option for optimal speed.
For architectural teams working with megapanels, controlling the aesthetic design of the megapanel can be complicated by the joints in the panels themselves (i.e., the panelization) and the positioning of the rainscreen joints of the external rainscreen. Ideally both types of joints would be carefully controlled as their impact on the aesthetics is so great. However, these are driven by issues such as transport, fabrication, installation, and procurement, and not left solely to the discretion of the architect.
On the McEvoy project, to coordinate joint locations and have a degree of control over façade’s appearance, the Design Team:
- Robustly modeled the megapanel and rainscreen joints in the Revit 3D model in a flexible way that could be documented in 2D.
- Communicated the design intent to a variety of different façade contractors at the early-stage tender.
- Responded to the selected facade subcontractor’s design and requirements and adjusted in the Revit model to further develop and coordinate the megapanel design.
There was an ongoing tension between the aesthetic requirements for a non-repetitive, non-gridded façade design and the cost and fabrication preferences for repetition; the new processes in Revit that were developed to best balance project drivers; and cost in terms of both Design Team fee and construction cost.
When considered separately, the individual drivers of the megapanels were simple. However, in aggregate, the combinations of drivers for each of the panels quickly became complicated. This made the process of modelling something in Revit that a subcontractor could eventually take over and fabricate difficult. Clearly communicating the design intent in a way that a subcontractor could understand and fabricate was a key goal of the design process, even from an early stage.
Background
The McEvoy and Dupont project is designed to provide much needed affordable housing in San Jose, California. The project is located at 699 West San Carlos Street near Diridon station
Access Restricted
Questions and Methods
Through the charrette and matrix development process the major drivers for the building envelope emerged as:
Product Quality– alignment with architectural goals, ability to meet performance requirements.Safety and Constructability -Access Restricted
Results & Discussion
One of the key questions of the documentation process had to do with finding the best way for the project to document the joints between the megapanels in the façade
Access Restricted
Conclusions
Megapanelization of facades is a novel approach that is likely to gain in popularity as the industry grows more familiar with the nuances of the system due to benefits of
Access Restricted
Rights and Permissions
REFERENCES
Figure 1: Sanborn Fire Insurance Map from San Jose, Santa Clara County, California. Sanborn Map Company, - Jan 1950; Vol. 2, 1950. Map. https://www.loc.gov/item/sanborn00817_007/.