Investigating Heat Development in Shadow Box Façade Systems
A Mock-up Test Approach for Follow-up Study
Presented on October 10, 2024 at Facade Tectonics 2024 World Congress
Sign in and Register
Create an Account
Overview
Abstract
The prevalence of fully glazed facades in modern office buildings has been steadily increasing, primarily driven by architects' focus on aesthetic appeal. While the desire for fully glazed designs with seamless transitions across buildings is evident, the shadow box, which consists of two layers of glass and an opaque back pan with an air cavity in between, stands out among other spandrel panel applications due to its unique visual effect on the facade. Architects frequently opt for the shadow box in designing the opaque sections of modern glass facades because these applications provide them with a high degree of design freedom. However, the shadow box is a complex system that requires precise design and manufacturing to prevent any negative impact on the overall building performance. It is susceptible to issues such as condensation, contamination, and overheating, which give rise to project-specific challenges for engineers and designers, adding complexity to detailing and real-life applications. This research constitutes the second phase of the study previously published for the ISCCGF – Zagreb 2023 Conference. Building upon the earlier work, this follow-up study employs a mock-up test approach to investigate the issue of overheating in shadow box systems.
The primary aim is to conduct extensive analysis of the underlying reasons for this problem. This will be achieved by utilizing the same test units while expanding both the dataset and the observation period. While the initial study mainly focused on type 3 shadow box behaviour, this current study addresses all shadow box types, drawing comparisons between them and re-examining the type 3 findings within a longer timeframe. The findings are expected to have considerable impact on future shadow box applications. Thus, the overall goal is to examine the behaviour of different shadow box settings and provide valuable information to the industry to overcome the potential problems faced in most projects. Moreover, the long-term goal is to contribute to the development of an enforceable consensus on shadow box applications in the industry, which currently does not exist.
Authors
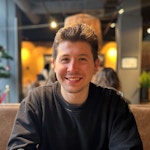
Ahmet Faruk Cakir
Master's Student in Facade Engineering and Werkstudent at Schüco
TH OWL
ahmet.cakir@stud.th-owl.de
Prof. Daniel Arztmann
Head of Custom Design International and Professor at TH OWL
Schüco International KG
darztmann@schueco.com
Keywords
Paper content
INTRODUCTION AND BACKGROUND
Curtain wall is a prominent component of contemporary architectural practice, as it gives an opportunity for architects to blend aesthetics and high-performance (Murray 2009). These systems comprise
Access Restricted
Acknowledgements
We express our gratitude to everyone who provided valuable comments and insights during the development of this research document. Special acknowledgment goes to AGC Glass Germany GmbH and Schüco International KG for their generous research funding, which significantly contributed to the completion of this project.
We also extend our sincere thanks to Godo Zabur Singh and Alvaro Balderema, whose pivotal roles in the initial study laid the foundation for this follow-up research. Their contributions have played a crucial role in shaping the direction and success of our work.
Rights and Permissions
Arztmann, Daniel. 2016. "Shadow Boxes – Re-Engineered: results from technical research and project design." Facade Tectonics Institute (Eds.), Facade Tectonics : World Congress Los Angeles 2016 Conference Proceedings, 2. Los Angeles: Tectonic Press. 10. https://www.facadetectonics.org/publications/collection/publications.
ASTM. 2020. “Standard Guide for Heated System Surface Conditions that Produce Contact Burn Injuries.” ASTM C1055-20, ASTM International, West Conshohocken, PA. DOI: 10.1520/C1055-20.
Bauer, Max, Armin Bäumler, and Martin Bauer. 2015. “Hinterlüftung Und Tauwasserausfall Bei Verbundfenstern.” Bauphysik 37 (4): 223–28. https://doi.org/10.1002/bapi.201510024.
Boswell, Keith and John Walker. 2005. "Shadow Boxes - An Architect and Cladding Designers’ Search for Solutions". Glass Processing Days 2005: Proceedings of the 9th International Conference, Tampere, Finland.
Brzezicki, Marcin. 2014. "Redundant transparency: The building's light-permeable disguise." Journal of Architectural and Planning Research.
Charles Pankow Foundation. 2023. "Thermal Performance of Spandrel assemblies in glazed wall systems." Phase 1: Design Test Program Final Report, Haymarket, VA, USA. https://www.pankowfoundation.org/site/assets/files/2320/04-22_thermal_performance_of_spandrel_assemblies_in_glazed_wall_systems-1.pdf.
Cucuzzella, Carmela, Negarsadat Rahimi, and Aristofanis Soulikias. 2023. "The Evolution of the Architectural Façade since 1950: A Contemporary Categorization" Architecture 3, no. 1: 1-32. https://doi.org/10.3390/architecture3010001.
CWCT. 2014. "Technical Note No.94 - Shadow Boxes." Centre for Window and Cladding Technology. https://www.cwct.co.uk/products/technical-note-94.
EN ISO. 2006. “Ergonomics of the thermal environment - Methods for the assessment of human responses to contact with surfaces - Part 1: Hot surfaces” EN ISO 13732-1:2006, ASTM International, BSI, Brussels, BE. DOI: https://dx.doi.org/10.31030/1471484.
Haldimann, Matthias, Andreas Luible, and Mauro Overend. 2008. “Structural Use of Glass.” International Association for Bridge and Structural Engineering IABSE, January. https://doi.org/10.2749/sed010.
Kragh, Mikkel. 2014. "Performance of Shadow Boxes in Curtain Wall Assemblies." CTBUH 2014 Shanghai Conference Proceedings. 6.
Lang, Andy. 2010. "Design Considerations for Shadow Boxes in Curtain Wall Glazing." ICBEST 2010 Conference Proceedings, 2.
McCowan, Derek, Mark Brown, and Micheal Louis. 2008. “Curtain-Wall Designs.” Glass Magazine. May 28, 2008. https://www.glassmagazine.com/article/curtain-wall-designs.
Murray, Scott Charles. 2009. Contemporary Curtain Wall Architecture. 1st ed. New York: Princeton Architectural Press.
Pilkington. 2012. "Technical Bulletin - Spandrel Panel Glazing ATS-124." ATS-124, Pilkington North America Inc., Toledo, OH, USA. https://www.pilkington.com/en/us/window-manufacturers/technical-bulletins#
Saint-Gobain. 2018. "Thermal Safety 3A: The resistance of glass to thermal Stress" Saint-Gobain Building Glass, UK.
Schwartz, Julien, Patrick Roppel, Stephane Hoffman, Neil Norris.. 2017. " Quantifying The Benefit of Venting Glazed Spandrels to Reduce Glass Breakage and Control Moisture." 15th Canadian Conference on Building Science and Technology Proceedings, Vancouver, BC, Canada.
Singh, Godo Zabur, Daniel Arztmann, and Alvaro Balderrama. 2023. “Investigating Heat Development in Shadow Box Façade Systems: A Mockup Test Approach.” ISCCGF- Zagreb 2023 Conference Proceedings. University of Zagreb, Faculty of Architecture. Zagreb, Croatia.
“Sunrise and Sunset Times in Berlin, June 2022.” n.d. https://www.timeanddate.com/sun/germany/bielefeld?month=6&year=2022.
“Thermal Stress: Film-to-Glass Compatibility.” 2012. EWFA. November 14, 2012. https://www.glassonweb.com/article/thermal-stress-film-glass-compatibility.
Walsh, Mark. 2018. "To Vent Or Not To Vent." Facade Tectonics Institute (Eds.), Facade Tectonics : World Congress Los Angeles 2018 Conference Proceedings, 2. Los Angeles: Tectonic Press. 10. https://www.facadetectonics.org/publications/collection/publications.