Interstitial condensation risk assessment
A three-dimensional steady-state tool
Presented on
October 9, 2024
at Facade Tectonics 2024 World Congress
Presented on
October 9, 2024
at Facade Tectonics 2024 World Congress
Presented on
October 9, 2024
at Facade Tectonics 2024 World Congress
Sign in and Register
Create an Account
Overview
Abstract
The development of methods to predict and control moisture accumulation in building envelopes has always been a key element in building science. Today’s existing hygrothermal engineering tools range from simple 1D steady-state heat and vapour transport models (widely known as the GLASER method) up to fully-coupled 2D and even 3D transient Heat Air and Moisture models. There is of course a trade-off between ease-of-use and accuracy. When hygric inertia, air transport or 2D/3D effects play a major role, predictions based on the 1D Glaser method (as standardised in EN ISO 13788) drift aways from reality. To obtain more realistic results, one should move to more advanced hygrothermal models considering the mentioned effects. When correctly used, advanced hygrothermal simulation result in highly detailed results. However, these advanced hygrothermal models often are considered too complex for day-to-day engineering work in the early design stage.
To fill this gap, the present article presents a practical 3D heat and vapour model to estimate the risk for interstitial condensation in building enclosures. The model is in fact a three-dimensional implementation of the Glaser method, including the calculation of moisture accumulation and drying in consecutive monthly periods.
The first part of this article outlines the modelling assumptions and solution technique. Thereafter, the model is validated against a 2D example from the literature and the 1D example from EN ISO 13788.
The article ends with an actual case whereby the applicability of the model is demonstrated by making design decisions for the energy-efficient retrofit of a curtain wall system.
Authors
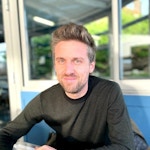
Jelle Langmans
Partner at Physibel
jelle.langmans@physibel.be
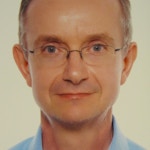
Piet Houthuys
Senior developer at Physibel
piet.houthuys@physibel.be
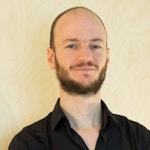
Wout Parys
Partner at Physibel
wout.parys@physibel.be
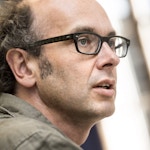
Staf Roels
Full professor at KU Leuven
gustaaf.roels@kuleuven.be
Keywords
Paper content
1. Introduction
Damage caused by moisture is a significant factor contributing to the degradation and diminished thermal performance of building components. Consequently, the development of tools to forecast and manage
Access Restricted
Rights and Permissions
[1] H. Janssen, The influence of soil moisture transfer on building heat loss via the ground. PhD thesis, Catholic University of Leuven, Departement of Civil Engineering, July 2002.
[2] H. M. Künzel, “Simultaneous Heat and Moisture Transport in Building Components: One- and two-dimensional calculation using simple parameters,” tech. rep., Fraunhofer IRB Verlag Stuttgart, 1995.
[3] C. Rode Pedersen, Combined heat and moisture transfer in building constructions. PhD thesis, Technical Uni-versity of Denmark, Lyngby, 1990
[4] A. Nicolai, Modelling and numerical simulation of salt transport and phase transitions in unsaturated porous building materials. PhD thesis, Syracuse University, Departement of Mechanical Engineering,
[5] A. Janssens, Reliable Control of Interstitial Condensation in Lightweight Roof Systems: Calculation and As-sessemnt Methods. PhD thesis, Katholieke Universiteit Leuven, 1998.
[6] C. E. Hagentoft, A. S. Kalagasidis, B. Adl-Zarrabi, S. Roels, J. Carmeliet, H. Hens, J. Grunewald, M. Funk, R. Becker, D. Shamir, O. Adan, H. Brocken, K. Kumaran, and R. Djebbar, Assessment Method of Numerical Prediction Models for Combined Heat, Air and Moisture Transfer in Building Components: Benchmarks for One-dimensional Cases, Journal of Thermal Envelope and Building Science, vol. 27, pp. 327–352, Apr. 2004.
[7] C.-E. Hagentoft, “HAMSTAD: WP2: Benchmark package,” tech. rep., University of Technology, Chalmers, 2002.
[8] EN ISO 13788 (2012) Hygrothermal performance of building components and building elements — Internal surface temperature to avoid critical surface humidity and interstitial condensation — Calculation methods
[9] TRISCO manual, https://www.physibel.be
[10] N. Simões, F.G. Branco A.Tadeu, Definition of two-dimensional condensation via BEM, using the Glaser method approach, Engineering Analysis with Boundary Elements 26(6):527-536, 2002
[11] J.F Straube and E.F.P Burnett, Chapter 5, ASTM Manual 40-Moisture Analysis and Condensation Control in Building Envelopes, American Society of Testing and Materials, Philadelphia, 2001