Integrated Building Control System
Field Deployment and Evaluation of Integrated Building Control System for Office Buildings
Presented on October 10, 2024 at Facade Tectonics 2024 World Congress
Sign in and Register
Create an Account
Overview
Abstract
Integrated management of commercial lighting, heating, ventilation and air conditioning systems is considered as one of the most promising building energy-efficiency and demand management strategies. A traditional approach to building automation includes a collection of independent control systems, one for each building end use, with limited or no communication among individual systems or devices such as electric lighting, shading, fenestration, some process loads and HVAC systems.
Significant research has been completed to improve the overall energy-efficiency of end-use devices and reduce operating hours through automated control. However, few accounted for the interdependence of lighting, fenestration and HVAC systems in an effort to improve the overall indoor environment.
The project goal was to refine, install and evaluate a pre-commercial Integrated Building Control System (IBCS) under real-world conditions to demonstrate the feasibility of an integrated controls approach and validate its potential for improving commercial building energy efficiency and demand flexibility. To do this, the project established a communication platform that lighting, fenestration and HVAC industries, refined control algorithms to optimize the performance of the individual building systems with respect to energy savings and occupant comfort, and verified system operation and costs in a real-world building.
A small-scale IBCS was installed and tested in a laboratory space equipped with an HVAC unit, an actuated window, actuated roller shades, 2x4 LED troffers, and a suite of various monitoring and control devices. After the lab test, the IBCS was deployed in a 2,068 sf office building at UC Davis campus.
The field deployment and building energy modeling results verified system design, procurement, installation and commissioning under real-world conditions for the new technology at scale. Project outcomes show that the IBCS can reduce HVAC, lighting and shading loads by 10 to 40 percent over typical baseline systems depending on building application, size, location, geometry and climate zone.
Authors
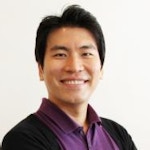
Jae Yong Suk, Ph.D.
Associate Professor of Design, Associate Director of California Lighting Technology Center
University of California, Davis
jysuk@ucdavis.edu
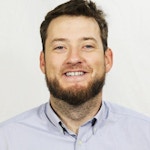
Keith Graeber, PE
Director of Engineering
University of California, Davis
kegraeber@ucdavis.edu
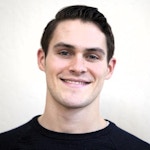
Andrew Harper, PE
R&D Engineer IV
University of California, Davis
agharper@ucdavis.edu
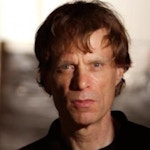
Michael Siminovitch, Ph.D.
Director of California Lighting Technology Center
University of California, Davis
mjsiminovitch@ucdavis.edu
Keywords
Paper content
INTRODUCTION
A traditional approach to building automation includes a collection of independent control systems, one for each building end use, with limited or no communication among individual systems or
Access Restricted
Acknowledgements
This project was supported by the California Energy Commission's Energy Research and Development Division.
Rights and Permissions
Choi, Joon-Ho, Vivian Loftness, Danny Nou, and Brandon Tinianov. “Impacts of Dynamic Glazing on Office Workers’ Environmental and Psychological Responses.” Architectural Research Centers Consortium (ARCC) conference, Toronto, Canada (2019)
Ing, Jennifer and Christopher Perry. “Smart Buildings: Using Smart Technology to Save Energy in Existing Buildings.” American Council for an Energy Efficient Economy (2017)
Konis, Kyle. “Evaluating daylighting effectiveness and occupant visual comfort in a side-lit open-plan office buildings in San Francisco, California.” Building and Environment 59 (2013): 662-677
Ghaffarianhoseini, Amirhosein, Umberto Berardi, Husam AlWaer, Seongju Chang, Edward Halawa, Ali Ghaffarianhoseini, and Derek Clements-Croome. “What is an intelligent building? Analysis of recent interpretations from an international perspective.” Architectural Science Review Volume 59 Issue 5 (2016)
Hirning, Michael, Gillian Isoardi, Coyne S, Ian Cowling, and Veronica Garcia-Hansen. “Post occupancy evaluation relating to discomfort glare: A study of green buildings in Brisbane.” Building and Environment 59 (2013): 349-357
Hirning, Michael, Gillian Isoardi, and Ian Cowling. “Discomfort glare in open plan green buildings.” Energy and Buildings 70 (2014): 427-440
Montier, Cedric du, Andre Potvin, and Claude MH Demers, “Energy and daylighting potential for Adaptive Façades: Evaluation of movable insulated panels” Proceeding of International Conference on Adaptation and Movement in Architecture, Toronto, Canada (2013)
Shen, Lester S., Masureen Colburn, Brad Kult, Luis Suau, and Matthew Schwartz. “Intelligent Building Technologies: A Technical Overview.” Center for Energy and Environment (2021)
Suk, Jae Yong and Marc Schiler. “Investigation of Evalglare Software, Daylight Glare Probability and High Dynamic Range Imaging for Daylight Glare Analysis.” Lighting Research and Technology (2012)
Suk, Jae Yong, Marc Schiler, and Karen Kensek. “Development of new daylight glare analysis methodology using absolute glare factor and relative glare factor.” Energy and Buildings 64 (2013): 113-122
Wu, Yujie, Jerome H. Kampf, and Jean-Louis Scartezzini. “Automated 'Eye-sight' Venetian Blinds based on an Embedded Photometric Device with Real-time Daylighting Computing.” Applied Energy v.252 (2019)
Lee, Eleanor and Stephen Selkowitz. "Design and Performance of an Integrated Lighting Envelope/Lighting System". https://eta-publications.lbl.gov/sites/default/files/39729.pdf. Lawrence Berkeley National Laboratory (1997)
Iddon, Christopher and Nikhil ParasuRaman. "Nightly Purge as a Means to Reduce Cooling Load in an Office in Pune, India". http://www.ibpsa.org/proceedings/BS2015/p2323.pdf. Proceedings of BS2015: 14th Conference of International Building Performance Simulation Association, Hyderabad, India, Dec. 7-9, (2015)