Insulating Glass Unit Gas Loss
Estimating the Effects on Cavity Widths
Presented on October 13, 2022 at Facade Tectonics 2022 World Congress
Sign in and Register
Create an Account
Overview
Abstract
Concerns over time-dependent argon permeation through the perimeter edge seals of insulating glass units (IGUs) led the authors to utilize two commercially available software packages to estimate the effects of net gas loss (including outflow and inflow of gasses) on IGU center-of-glass cavity widths. In both cases, the primary consideration was maintaining the ideal gas law within the cavity width(s). Both double and triple glazed IGUs were modeled.
The code for one software package (developed in part by one of the authors) was modified to include net percentage loss of original gas quantity (i.e., net loss of gas moles) as an input parameter. Recognizing that percentage loss of moles (n) and percentage loss of temperature (T) should cause the same effect on the IGU cavity width, the second software package was utilized in its commercially available form, which included input parameters for temperature differentials within the cavity.
The two approaches compare favorably for both double and triple glazed IGUs experiencing gas loss within one cavity, with and without wind load. Using an iterative procedure, the percent loss of specific fill gasses (e.g., argon) can be calculated for a given net gas loss. The effects of gas loss can also be combined with climatic effects to determine the likelihood of individual glass lites within the IGU touching at some point in the future (assuming cumulative net gas loss with time).
The techniques utilized by the authors are beneficial for forensic evaluations, as well as facade designs that aim to limit reflected distortion by maintaining relatively flat exterior glass lites.
Authors
Mark K. Schmidt, M.Eng., S.E.
Principal and Unit Manager
Wiss, Janney, Elstner Associates (WJE), Inc.
mschmidt@wje.com
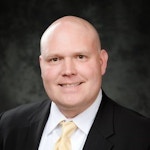
Stephen M. Morse, PhD, P.E.
Assistant Professor
Michigan Tech University
smmorse@mtu.edu
Keywords
Introduction
Insulating glass units are the prominent type of window infill panels used in commercial and residential facades due to their enhanced thermal performance over single lites. Insulating glass units (IGUs) are composed of two or more lites (monolithic or laminated) separated by a spacer (aluminum, steel, foam, etc.) and adhered together by one or more sealants. The presence of the sealed cavity created by the spacer provides the primary increase in thermal performance, in addition to having more glass surfaces available for application of low-emissivity (low-e) coatings. A secondary performance enhancement due to the sealed air space is the sharing of applied loads (e.g., wind load) between the individual glass lites. Common practice for determining the load sharing and resulting load resistance for IGUs utilizes a simplistic model based only on the lite thicknesses, even though many other factors are known to affect the structural behavior of IGUs including: air space thickness, temperature, initial pressure; type of gas contained in the air space, nonlinear mechanical behavior of plates, edge rotation fixity due to the sealant holding the unit together, and atmospheric pressure at the installation site, among others.
Depending on the IGU geometric configuration and installation site, undesirable performance issues can arise such as pillowing (inward or outward) where the lites comprising the IGU do not remain parallel. Pillowing of IGUs is due to net pressure differentials across the IGU caused by changes in temperature, atmospheric pressure, or both. In extreme cases, the lites can also deform into the cavity to such an extent that glass-to-glass contact occurs. Historically, this extreme case of pillowing has been assumed to be rare, however several recent documented cases involving large commercial-sized IGUs have had lites contacting each other.
Several scenarios are known to cause pillowing, most common is changes in atmospheric pressure due to elevation changes between the IGU assembly location and the installation site, periodic weather fronts and large changes in atmospheric temperature. These known scenarios can generally be analyzed using commercially available glass design software. Other sources of apparent pillowing can be due to bow or warping of one or more lites comprising the IGU, where, in the worst case, the lites are oriented in such a manner that the cavity width is minimized (i.e., both lites bowing inward into the cavity). However, standard IGU manufacturer QA/QC procedures could identify IGUs with unacceptable cavity widths before they are shipped to the project site. Furthermore, the effects of glass bow on the center-of-glass cavity width can be determined by measuring the IGUs after fabrication and before gas filling in general conformance with the procedure given in IGMA TM-4400-18 [2].
Another potential cause of pillowing that can occur during IGU fabrication is improper gas filling causing unintentional internal cavity pressures (assuming no intentional cavity width compensation measures are employed). Again, this condition could be detected by QA/QC procedures that involve measuring center-of-glass cavity widths before and after gas filling. While the individual effects of atmospheric pressure/temperature changes, bowed glass, or improper gas filling may not result in lite contact, a combination of two or more effects might cause this phenomenon.
In the aforementioned cases, the amount of gas in the cavity is assumed to be constant, and the interaction of the lites and the cavity space are directly related to the Ideal Gas law. However, certain gases used to fill the cavity to enhance the thermal performance of the IGUs are known to permeate the IGU sealant. Argonomics [3] provides initial volumetric flow rates of gas exchange through the IGU perimeter seal for the most commonly used gas fill, argon, and the atmospheric gasses (oxygen and nitrogen) for an assumed 100 percent initial argon fill of typical commercial IGUs. Argonmics does not provide volumetric flow rates for other initial gas concentrations, nor does it describe the changing effect of progressive argon loss on volumetric flow rates. Regardless of the specific theory governing the argon loss, the outflow of argon without a similar inflow of nitrogen and oxygen would cause a resulting pressure differential and a reduction of the center-of-glass cavity width..
To determine the effect of argon permeation on the IGU cavity width, an analytical technique capable of changing the amount of gas contained in an IGU cavity would be required; however, commercially available software for designing/analyzing IGUs do not currently provide this option a. This paper explores two options for modifying commercially available glass software packages to simulate changes in the cavity gas amounts to explore the related effects on the center-of-glass cavity widths. The two approaches are described herein and several IGU constructions are analyzed for varying degrees of cavity gas loss.
Ideal Gas Law
The ideal gas law is employed to handle the interaction between the sealed cavity and the lites of an IGU for changes in temperature, pressure and volume; provided here for
Access Restricted
Analytical Methods to Estimate IGU Cavity Widths for Various Net Gas Losses
AWGD Modifications
Advanced Window Glass Design (AWGD) by the Standards Design Group [6], which was developed in part by one of the authors, has the functionality to change climatic conditions
Access Restricted
Net Gas Loss Relation to Loss of Fill Gas
The net gas loss analyses described above can be utilized to determine the loss required to cause contact between glass lites. This net gas loss can then be utilized in
Access Restricted
Next Steps
The approaches described above can also be utilized to determine the loss of fill gas (e.g., argon or krypton) in combination with climatic effects (changes in temperature and pressure from
Access Restricted
Rights and Permissions
[1] ASTM, 2016. “Standard Practice for Determining Load Resistance of Glass in Buildings.” ASTM E1300-16, West Conshohocken, Pennsylvania, USA.
[2] IGMA, 2018. “Voluntary Guidelines for Insulating Glass Unit Cavity Width Manufacturing Tolerances.” Insulating Glass Manufacturers Alliance, TM-4400-18, Chicago, Illinois, USA.
[3] Vitro, 2016. “Argonomics.” Vitro Flat Glass, Glass Technical Document TD-126, Cheswick, Pennsylvania, USA.
[4] Vallabhan, C.V.G., Chou, G.D., 1986. “Interactive nonlinear analysis of insulating glass units.” J. Struct. Eng. 112(6), 1313–1326.
[5] Morse, S.M. and Norville, S.N. 2016. "Comparison of methods to determine load sharing of insulating glass units for environmental loads." Glass Struct. Eng. (1), 315-329.
[6] Standards Design Group, 2022. “Advanced Window Glass Design”, https://standardsdesign.com/advanced-window-glass-design.
[7] SJ Software GmbH, 2022. “SJ Mepla”, https://www.mepla.net/en/