Glass Strength Under Point Loading
Parametric Determination of Probability of Breakage for Typical Panel Dimensions
Sign in and Register
Create an Account
Overview
Abstract
Structural glass is used in a range of building applications, and while the ASTM E1300 has recently been updated to provide a design method to account for probabilistic failure models for a range of geometries under uniform loads, there does not exist detailed design information for point loads. While, ASTM E2751 provides an allowable stress based on a theoretical probability of breakage (POB) of 8/1000 from the appendix of ASTM E1300, these allowable stresses have only a loose correlation to POB and are not accurate for all glass configurations. To address this, the authors explore the effect of point loads on glass strength using the glass failure prediction model (GFPM) from E1300 to determines the allowable stress (or allowable load) for common glass lite geometry based on a POB of 8/1000 and 1/1000. Results allow practitioners to benchmark designs for monolithic and PVB laminated glass based on various point-support boundary conditions.
The parametric study investigates the maximum principle stresses and stress concentrations of specimen types subjected to out-of-plane bending due to a point load over 26 cm2(4 in2).The maximum point load is found for various 4-side supported glass lites at a POB of 8/1000 and 1/1000.
Authors
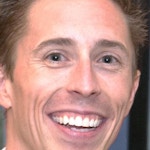
Joshua Schultz, Ph.D, P.E., LEED AP, ENV SP
Assistant Professor
Gonzaga University
schultzj@gonzaga.edu
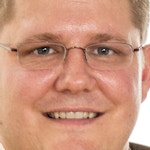
John Knowles, PE SE
Vice President
Stutzki Engineering
john.knowles@stutzkiengineering.com
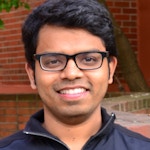
Kedar Malusare
Stutzki Engineering
kedar.malusare@stutzkiengineering.com
Keywords
Introduction
Structural glass applications, particularly façade and canopy elements, continue to grow in ubiquity as transparency and daylighting remain significant motivators of architectural design. However, current design procedures (i.e., elasticity and plate theories) and US design standards (e.g. ASTM E1300, 2016) are not directly applicable to structural glass with concentrated point loading. While ASTM E2751 (2017) does address point loads as design considerations it lacks a clear approach to determining strength, instead referencing ASTM E1300. The lack of clear design criteria for glass applications with point loading has resulted in designers relying on stress distributions and single largest maximum principle tensile stress (SLMPTS) as a guide for acceptable behavior which is often either unconservative or over-conservative – even when using low ultimate stress values to dictate design thicknesses. Development of the most recent ASTM E1300 has changed the approach to a range of structural glass applications due to the probabilistic-based failure prediction method explicitly presented in Annex A2, coupled with the acceptance of numerical modeling to obtain stresses and stress distributions. While the current ASTM E1300-16 still only contains non-factored load (NFL) charts for uniformly distributed loads, it is possible to establish a set of plots similar to those found in Annex A1 using the methodology presented in Annex A2. In an effort to provide meaningful design criteria to engineers and architects alike, a statistical glass failure prediction model (GFPM) is applied finite element analysis (FEA) data to provide design strength results for annealed and heat-strengthened (HS) specimens under point loading that provide a probability of breakage (POB) of 1 in 1,000 and 8 in 1,000, respectively. GFPM results are intended to 1) allow practitioners to benchmark designs for Annealed and HS monolithic glass based on various geometric conditions 2) provide strength of annealed and HS specimens for POB of 1/1000 and 8/1000 and 3) serve as a baseline methodology for more comprehensive, on-going efforts to create complete tables for designers. Additionally, a detailed description of the GFPM is provided with background information in order to assist designers with understanding of the necessity of a rigorous POB-based design approach compared to sole reliance on the SLMPTS.
The growth of glass as a façade component includes applications of skylights, glass floors and curtain walls. The industry trend is to produce larger glass lites to increase transparency and by extension the natural lite and sight lines inside the building. As the need for larger glass is desired, loads from human impact have greater consequences than in the traditional applications of smaller glass panels. Impact loads can come from accidental impact from nearby pedestrians or impact while cleaning. For example, the Virginia Tech curtain wall (Fig. 1A), University of Baltimore curtain wall (Fig. 1B) which is subject to regular cleaning, University of Chicago Biomedical School glass wall with floor to ceiling glass (Fig. 1C) and the large line-supported glass panels of the American Girl Doll Store (Fig. 1D) each have considerable design differences, but all required consideration of an applied point load due to the large areas of glass which increase probability of breakage (POB).
A more obvious example would be the skylight glass used on the roof of the Aspen Art Museum, which also is designed for pedestrian traffic (Fig. 2). This skylight needs to consider the concentrated point loads specified in ASTM E2751 (Standard Practice for Design and Performance of Supported Glass Walkways) and references ASTM E1300 for calculation guidance, but the design charts in ASTM E1300 (Standard Practice for Determining Load Resistance of Glass in Buildings) are for uniform loads only.
In order to address this design gap, the GFPM is applied to two common glass types (annealed and HS glass) and a range of aspect ratios using the same considerations as the provisions in the commonly referenced ASTM E1300 standard, but focuses on the unique results for point-loading as described in ASTM E2751. This method incorporates the relevant parameters (stress concentration due to Griffith surface flaws, load-duration effects, humidity, residual compressive surface stress, etc.,) on the principle stresses in order to provide designers with design strengths for specific POB for glass panels with point loads.
Literature Review on Probabilistic Glass Failure
In the United States, most structural glass is currently designed either directly or indirectly according to ASTM E1300 (2016). The nonfactored load (NFL) design charts in Annex A1 of E1300 allow for quick selection of minimum thickness for given panel geometry and desired load resistance of annealed glass. Design thicknesses for other glass types (heat strengthened (HS), fully tempered (FT), laminated glass (LG), insulating glass (IG), wired, and etched) are readily achieved by application of modification factors to the annealed selection. While this procedure appears straightforward, it is essential that designers understand the assumptions and limitations of the method. For example, the design charts in Annex A1 of ASTM E1300 are specifically for determination of the minimum thickness of window glass and are explicitly limited to rectangular geometries with a uniform load that are simply supported along at least one edge. Additionally, Appendix X6 offers “conservative” allowable stresses for use with finite element analysis for atypical glass geometries. However, the source of these “conservative” values is unknown, and there is only a loose correlation between these allowable stresses and actual POB of the glass lite. Since this limitation extends only to the charts in Annex A1 and not the procedure of Annex A2 it is important for designers to understand both the theory behind the design charts and methodology presented in ASTM E1300. The glass failure prediction model (GFPM) that serves as the basis for the NFL charts is used in this research to develop design strengths for POB of 1 in 1,000 and 8 in 1,000 for annealed and HS rectangular lites exposed to point loads. The efficient design of a brittle material with statistical failure behavior (i.e., glass) requires an accurate determination of a multitude of factors: SLMPTS, stress distributions, surface flaw characterization, residual compressive surface stress (RCSS), load-duration, temperature and humidity effects, etc (Schultz et al., 2017). In order to accurately use the ASTM E1300 design method it is important to understand each term and how it has been integrated into the procedure over time.
The brittle and probabilistic nature of glass as a material means that it often fails under stresses significantly lower than the ultimate stress. As early as 1920, it was hypothesized that this was a result of microscopic surface flaws that created stress concentrations which promoted crack growth (Griffith, 1920). Evidence of this behavior was readily observed in failures of all glass types, as the initiation of the failure was often not coincident with the SLMPTS (Natividad et al., 2015). The distribution and orientation of these surface flaws was modeled using the statistical multiple parameter fitting method presented by Weibull (1939). In addition to surface flaws, subsequent research attributed the apparent reduction in annealed glass strength to load duration and presence of humidity (Charles 1958). Many experimental initiatives tested annealed and HS glass specimens to failure in an effort to quantify this behavior (Orr, 1957; Bowles and Sugarman, 1962). The results of these tests combined with successful empirical designs formed the basis for a series of design guidelines developed by the glass industry for window glass in the early to mid-1960s.
A significant change in glass design occurred when Beason and Morgan (1984) combined the effects of surface flaws (orientation and distribution) and humidity into a single glass failure prediction method (GFPM) using a two parameter Weibull distribution and determination of SLMPTS based on the work of Vallabhan et al., (1985, 1987). This research reframed glass strength fully in terms of probability of breakage (POB) rather than ultimate strengths (which were readily mistaken for a type of allowable stress design). The method developed by Beason and Morgan assumes that the glass strength is 1) governed by tensile stress failure and 2) independent of load duration (not necessarily an accurate assumption for all types of glass, i.e., laminated glass). This methodology served (and continues to serve) as the fundamental design approach for glass design procedures and charts in every ASTM E1300 standard from 1989 to 2016. However, subsequent research by Morse and Norville (2011, 2012) has relaxed assumptions of glass type (annealed, HS and FT) and geometry used in the ASTM E1300 charts by creating more general forms of the GFPM equation. In fact, Morse and Norville (2012) presented the explicit form of the risk function, B, not found in ASTM E1300, used by Walker and Muir (1984) for consideration of edge flaws in annealed glass fins. More recently, Afolabi, Norville and Morse (2016) provided a detailed experimental study of HS line supported glass with discussion of RCSS and equivalent failure load (EFL). However, none of these studies focused on point-loads. There has been some research into the aapplication of the GFPM to non-traditional applications like point-supported glass (PSG) was addressed by Cervenka et al., (2016). That research focused on experimental stresses and stress distribution near holes in monolithic and laminated FT glass to determine influence of stress concentrations. The work was extended by Schultz et al., (2017) to create 3-second failure load curves and determination of best-fit m- and k-values for PSG.
Method
A series of parametric finite element models were run using Abaqus FEA software (Abaqus, 2017) to obtain the maximum principle stresses and stress distributions. The modeling approach followed the methods
Access Restricted
Data
Maximum, deflections, U, principle stresses, S1, and stress distributions were found for the rectangular panels of varying aspect ratios (Figs 4-6). The stress distributions and deflected shapes of the panels
Access Restricted
Explanation
The design loads and related stresses presented in Figs 7-10, provide designers a simple reference for selection of geometries to meet desired POB for annealed and HS lites of 5.5
Access Restricted
Conclusion and Future Work
The results presented are for four side supported, 6 mm thick, annealed and HS glass types. Ongoing studies are being completed to build out a series of design tables for
Access Restricted
Acknowledgements
The authors gratefully acknowledge Stutzki Engineering for the use of images.
Rights and Permissions
ABAQUS: Multi-Purpose Finite Element Analysis Software, Dassault Systems. 2017
Afolabi, Bolaji, H. Scott Norville, and Stephen M. Morse. "Experimental study of weathered tempered glass plates from the Northeastern United States." Journal of Architectural Engineering 22, no. 3 (2016): 04016010.
ASTM International. ASTM E1300-16 Standard practice for determining load resistance of glass in buildings. West Conshohocken, Pennsylvania, USA. ASTM; 2016. www.astm.org p. 1-62.
ASTM International. ASTM E2751-17a. Standard Practice for Design and Performance of Supported Glass Walkways. West Conshohocken, Pennsylvania, USA. ASTM; 2017. www.astm.org p. 1-8.
Beason, W. Lynn, and James R. Morgan. "Glass failure prediction model." Journal of Structural Engineering 110, no. 2 (1984): 197-212.
Bowles, R., and B. Sugarman. "The strength and deflection characteristics of large rectangular glass panels under uniform pressure." Glass Technology 3, no. 5 (1962): 156-170.
Cervenka, J., Schultz, J.A., Stahl, D., and Knowles, J. “Strength of point-supported glass.” In Proceedings of the 1st Facade Tectonics World Congress; Tectonics Press Publications., pp. 381-389. 2016.
Charles, R. J. "Static fatigue of glass. I and II." Journal of Applied Physics 29, no. 11 (1958): 1549-1553.
Griffith, Alan A. "The phenomena of rupture and flow in solids." Philosophical transactions of the royal society of london. Series A, containing papers of a mathematical or physical character 221 (1921): 163-198.
Morse, S. and Norville, H. “An analytical method for determining window glass strength.” In Proceedings of Glass Performance Days 2011; GPD Press 9; pp. 480-482. 2011.
Morse, Stephen M., and H. Scott Norville. "Design methodology for determining the load resistance of heat-treated window glass." Journal of Architectural Engineering18, no. 1 (2011): 42-51.
Natividad, Kayla, Stephen M. Morse, and H. Scott Norville. "Fracture Origins and Maximum Principal Stresses in Rectangular Glass Lites." Journal of Architectural Engineering 22, no. 2 (2015): 04015014.
Orr, Leighton. "Engineering properties of glass." Publication 478 (1957): 51-61. Bowles and Sugarman, 1962;
Schultz, J.A., Knowles, J., and Morse, S., “Glass Failure Prediction Model for Out-of-Plane Bending of Waterjet-Drilled Holes,” In Proceedings of the 39th IABSE Symposium, International Associated of Bridge and Structural Engineers, Vancouver, Canada. 2017.
Schultz, Joshua, Douglas Stahl, and Christian Stutzki. "Experimental investigation of numerical design method for point-supported glass." Journal of Architectural Engineering18, no. 3 (2012): 223-232.
Vallabhan, CV Girija, Bob Yao-Ting Wang, Gee David Chou, and Joseph E. Minor. "Thin glass plates on elastic supports." Journal of Structural Engineering 111, no. 11 (1985): 2416-2426.
Vallabhan, CV Girija, Joseph E. Minor, and Sesha R. Nagalla. "Stresses in layered glass units and monolithic glass plates." Journal of structural Engineering 113, no. 1 (1987): 36-43.
Walker, G. R., and L. H. Muir. "Investigation of the Bending Strength of Glass Louvre Blades." In Ninth Australasian Conference on the Mechanics of Structures and Materials, ACMSM 9., pp. 122-126. 1984.
Weibull, Waloddi. "A statistical theory of the strength of materials." Ingeniors Vetenskaps Akademien (1939).