Structural Silicone Sealant and Glass Fins
Exploring 3-Sided Adhesion
Presented on October 10, 2024 at Facade Tectonics 2024 World Congress
Sign in and Register
Create an Account
Overview
Abstract
Structural silicone sealant is commonly used in glass fin applications, both as a weatherseal and as for structural attachment. A common concern for sealants in construction applications can be the potential for 3-sided attachment which can limit the freedom of movement in a joint. Potential design geometries were analyzed via finite element analysis to illustrate how limiting movement can be beneficial for structural elements.
Authors
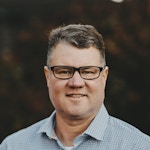
Jon Kimberlain
Principal TS&D Scientist
Dow
jon.kimberlain@dow.com
Valerie Hayez
Principal TS&D Scientist
Dow
valerie.hayez@dow.com
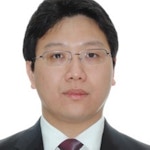
Jie Feng
Research Scientist
Dow
jfeng2@dow.com
Keywords
Paper content
Introduction
Three-sided bonding refers to the potential for a sealant joint, typically rectilinear in shape, to be in adhesive contact on three sides of the geometry which will constrain
Access Restricted
Rights and Permissions
ASTM C719 Standard Test Method for Adhesion and Cohesion of Elastomeric Joint Sealants Under Cyclic Movement (Hockman Cycle), ASTM International, West Conshohocken, PA, 2014, www.astm.org
ASTM C920, Standard Specification for Elastomeric Joint Sealants, ASTM International, West Conshohocken, PA, 2014, www.astm.org