Fit for the Future
Sustainable 3D printed building facades
Presented on October 10, 2024 at Facade Tectonics 2024 World Congress
Sign in and Register
Create an Account
Overview
Abstract
Wearables protect us from climatic conditions, they provide privacy, comfort and they also reflect our style and personality. Building facades in the same way, provide protection from the weather, comfort, privacy and showcase typology and style. The link between architecture and fashion is a perceptible phenomenon in both theory and practice through many contemporary pioneers including Frank Lloyd Wright, Adolf Loos, Coco Chanel and Joseph Hoffmann. Designing the architectural surface was frequently understood as being like designing a garment. The foundation of this connection between textiles or dresses and architecture had been laid in the mid-19th century by architect Gottfried Semper’s “Principle of Dressing”.
This research investigates the relationship of fashion and building skins and demonstrates how buildings of the future can have skins that are fit and performative and are 3D-printed with innovative sustainable materials. Across the world, temperature extremities are rising into previously unimagined realms, and our seasons are disrupted by record setting heat. Extreme heat affects health and wellbeing, and it affects how we occupy and use buildings. Ground-up construction will diminish in urban environments and increasingly be replaced with retrofits. Within this research the design of retrofits of existing buildings is being rethought, providing new wearable skins “Jackets for buildings”, which respond to extreme climatic conditions.
By addressing specific contemporary concerns in architectural facade design, the research method utilizes natural living systems as inspiration to develop new, creative and critical design techniques inspired by biomimicry. Aesthetically appealing catalogs of computational designs and 3D printed prototypes, made of biodegradable plastic, resin and binder jetting technologies demonstrate visually rich case studies for innovative and sustainable facade designs. The research provides opportunities to expand positions in architecture by rethinking existing problems, establishing new directions, and making well-informed and progressive conjectures that shape the built environment.
Limited publications about this topic exist in architecture literature since the topic is cutting edge and novel, situated in speculative design research for relevant future scenarios. Key audience are architecture educators, students, and industry leaders in facade design, technology and 3D printing building industries.
Authors
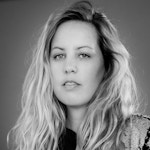
Julia Koerner-Al-Rawi
Associate Adjunct Professor, Director of Summer Programs, Department of Architecture and Urban Design
UCLA
juliakoerner@ucla.edu
Keywords
Paper content
Introduction and Contemporary Research Facts:
This research responds to today’s climatic crises by rethinking building skins and sustainable fabrication techniques and on the other hand explores how design qualities and
Access Restricted
Acknowledgements
The “Fit for the Future, Sustainable 3D printed building Facades” Research Studio was supported by the Charles Moore Travel Grant provided by UCLA, School of Arts and Architecture, Department of Architecture and Urban Design in 2022/23.
The following graduates of 2023 contributed to this research: Blake Hannah, Bryan Tyler, Chen Sandra Ren Shan, Cuevas Striekwold Miguel Stijn, He Leyi, He Xueqi, Jiang Yi, Long Lufeng, Qiu Rui, Rodriguez Daniel, Wang Yuzhou, Yang Frank
Special thanks to selected guest lecturers and critics:
Andreas Körner, Assistant Professor at University of Innsbruck
Isabelle Hens, Environmental Designer at Atelier Ten
Sophie Pennetier, Associate Director - Special Projects, ENCLOS
Kais Al-Rawi, Associate Director at Eckersley O’Callaghan’s Los Angeles office
Manuel Jimenez Garcia, co-founder, and CEO of Nagami
Melodie Yashar, VP of Building Design & Performance at ICON
Sofia Hagen, co-founder, and director of HagenHinderdael
Rights and Permissions
Photography by Photographer Sarah M. Golonka
Drawings by Graduate Students UCLA, AUD
Blake Hannah
Bryan Tyler
Chen Sandra Ren Shan
Cuevas Striekwold Miguel Stijn
He Leyi
He Xueqi
Jiang Yi
Long Lufeng
Qiu Rui
Rodriguez Daniel
Wang Yuzhou
Yang Frank