Exploring Interoperability between Rhino and Revit through Rhino.inside
A dual case study
Presented on October 10, 2024 at Facade Tectonics 2024 World Congress
Sign in and Register
Create an Account
Overview
Abstract
This paper presents a comprehensive interoperability workflow achieved between Rhino and Revit through Rhino-Inside. The study focuses on two case studies with different building type, where both of their curtainwalls utilize the integration of Rhino and Revit with two discrete workflow through Rhino-Inside. This integration enables the manipulations of Revit families through Grasshopper, seamlessly integrating a design platform with a BIM platform, harnessing the power of parametric design and data synchronization across platforms.
The first case study delves into a healthcare project that explores through modeling capabilities of Rhino, and interoperability of Rhino.inside, allowing a one-way lightweight import over to Revit. This case study demonstrates the potential for enhancing creativity and design exploration while keeping streamlined twin model for early phrase Revit development.
The second case study explores the Rhino-inside control further, where through Grasshopper, the Rhino model gets disassembled into the most basic understanding of Revit native curtainwalls, and leverages Rhino-inside to manipulate parameters on the model to establish a bidirectional data flow. This bidirectional data flow ensures that changes made in either Rhino or Revit are seamlessly integrated across both platforms, fostering a synchronized and updated project representation.
Through these two case studies, this paper highlights the transformative potential of the Rhino-Inside framework in enhancing interoperability between Rhino and Revit. The case study presents the significance of an integrated workflow that serves as a testament to the continual evolution of software interoperability, enabling professionals to explore innovative design solutions and streamline the design, BIM management, and construction documentation process.
Authors
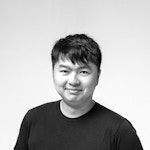
Vincent Ip
Associate / Designer / NBBJ DIGITAL - Studio DC Leader
NBBJ
sfxvincent@gmail.com
Keywords
Paper content
Figure 1: Physical Representation vs Level of Development(LOD) of a Revit Model in various phase and where Rhino/Grasshopper/Rhino.Inside ties into each phase
The field of architecture has seen an
Access Restricted
Acknowledgements
The author wish to acknowledge and thank the team in NBBJ Los Angeles, Boston and Hong Kong studio, especially Sam Keville and Leo Li.
All images are provided courtesy of the author and NBBJ unless otherwise stated.
Rights and Permissions
BIMForum (2023) 2023 Level of Development Specification Guide. http://bimforum.org/lod/. Accessed 20 January 2024
Ip, Vincent. “Managing Constraints- An Integrated Design to Construction Workflow”, Facade Tectonics 2020 World Congress,2020
Crolla, Kristof. “Building Simplexity – The expansion of digital design into “contractor space”, In W. Huang, Y. Liu, W. Xu (eds.), Digital Infiltration & Parametricism: Proceedings of the DADA2013 International Conference on Digital Architecture, 2013, Tsinghua University Publishing House, Beijing, 2013, pp. 30-40