Determination of Surface Flaw Parameters for Annealed and Fully Tempered Glass Exposed to NaCl
Presented on October 10, 2024 at Facade Tectonics 2024 World Congress
Sign in and Register
Create an Account
Overview
Abstract
The use of glass in the exterior facades provides greater light transmission into the building and improved views for occupants. Coastal areas in particular leverage the transparency of glass to maximize views. However, the innate characteristic of glass, due to the presence of microscopic flaws attributed to the manufacturing process and handling and weathering of glass, is to lose strength over time, a phenomenon known as static fatigue of glass. The strength of glass reduces due to the presence of water vapor and tensile stress. In the coastal areas, glass is exposed to sodium chloride (NaCl) from the sea, in addition to water vapor and tensile stress. To date, the effect of NaCl on glass has not been documented. This research presents the results from a study to observe the effect of NaCl on the strength of glass. The study loaded 39 glass specimens to failure using a three-point bending test. The glass specimens were 457 mm (18 in) long, 203 mm (8 in) wide, and of different thicknesses and were categorized into three samples based on the type of glass (i.e., annealed vs fully tempered, and 4.77 mm (0.375 in) vs 6.35 mm (0.25 in) thickness). To understand the effect of NaCl on the strength of glass, 20 specimens were loaded to failure at the time of receiving the specimen from the manufacturer, while 19 specimens were soaked in a NaCl solution for a full year before loading to failure. Surface flaw parameters for both sample sets were determined by applying the maximum likelihood estimator to the glass failure prediction model. Results for surface flaw parameters are presented for NaCl-treated and untreated specimens and sample strength was compared at 0.008 and 0.001 probability of breakage. Results did not exhibit a consistent trend; two sample sets showed a decrease in strength at both probabilities of breakage, while another sample showed an increase in strength, but further testing is recommended.
Authors
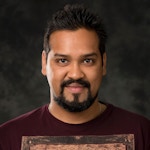
Nabhajit Goswami, PhD
Senior Facade Engineer
Thornton Thomasetti
ngoswami@thorntontomasetti.com
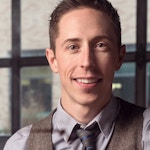
Joshua Schultz, PhD, PE, LEED AP
Associate Professor
Gonzaga University
schultzj@gonzaga.edu
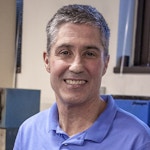
Patrick Ferro, PhD, PE, MBA
Professor
Gonzaga University
ferrop@gonzaga.edu
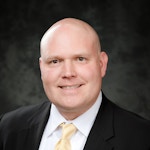
Stephen M Morse, PhD, PE
Associate Teaching Professor, Mechanical Engineering-Engineering Mechanics Affiliated Assistant Professor, Civil, Environmental, and Geospatial Engineering
Michigan Tech University
smmorse@mtu.edu
Keywords
Paper content
The popularity of glass as a building material, when compared to other building materials such as steel and concrete, is primarily due to its transparency which allows the passage of
Access Restricted
Rights and Permissions
REFERENCES
- Charles, R. J. (1958). Static fatigue of glass. II. Journal of Applied Physics, 29(11), 1554-1560.
- Wiederhorn, S., & Bolz, L. H. (1970). Stress corrosion and static fatigue of glass. Journal of the American Ceramic Society, 53(10), 543-548.
- ASTM Standard. (2016). ASTM E1300 Standard Practice for Determining Load Resistance of Glass in Buildings.
- Beason, W. L., & Morgan, J. R. (1984). Glass failure prediction model. Journal of Structural Engineering, 110(2), 197-212.
- Goswami, N., Schultz, J. A., Zhang, K., Dowden, D. M., Swartz, R. A., & Morse, S. M. (2023). Estimation of flaw parameters for holes in glass using maximum likelihood estimator. Glass Structures & Engineering, 8(3), 405-421.
- Weibull, W. (1939). A statistical theory of strength of materials. IVB-Handl.
- Norville, H. S., Bove, P. M., & Sheridan, D. L. (1991). The strength of new thermally tempered window glass lites. Glass Research and Testing Laboratory, Department of Civil Engineering, Texas Tech University.
- Morse, S., & Norville, H. (2011). An analytical method for determining window glass strength.
- Hausmann, B. D., & Salem, J. A. (2017). Effects of Aqueous Solutions on Slow Crack Growth of Soda Lime Silicate Glass. Mechanical Properties and Performance of Engineering Ceramics and Composites XI: Ceramic Engineering and Science Proceedings Volume 37, Issue 2, 37, 45-52.
- Brown, W. G. (1974). A practicable formulation for the strength of glass and its special application to large plates. National Research Council Canada.
- Afolabi, B., Norville, H. S., & Morse, S. M. (2016). Experimental study of weathered tempered glass plates from the Northeastern United States. Journal of Architectural Engineering, 22(3), 04016010.
- Fothergill, J. C. (1990). Estimating the cumulative probability of failure data points to be plotted on Weibull and other probability paper. IEEE Transactions on Electrical Insulation, 25(3), 489-492.