Blast Performance
Modeling Case Study of SSG
Presented on October 9, 2024 at Facade Tectonics 2024 World Congress
Sign in and Register
Create an Account
Overview
Abstract
Designing for blast performance for glazing units can be very complex. The test methods for evaluating performance include subjecting units to actual or simulated blast conditions, which occur rapidly on a very short time scale. Connecting laminated glass to a metal frame using structural silicone sealant creates a unique composite based on the use of a brittle plate with an elastic soft rubber to a ductile rigid metal.
Glazed units were tested with a shock tube charged with various levels of explosive to record the damage development with various modes of failure of the material. Two test results were modeled to compare to the actual observations. Based on the outcome, techniques for effective modeling are discussed as well as future needs.
Authors
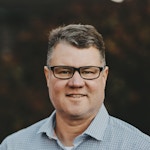
Jon Kimberlain
Principal TS&D Scientist
Dow
jon.kimberlain@dow.com
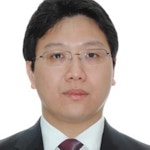
Jie Feng
Research Scientist
Dow
jiefeng2@dow.com
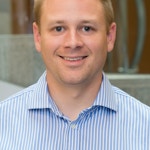
Will Wholey
Associate
Arup
will.wholey@arup.com
Dan Aggromito
Senior Consultant
Arup
Daniel.Aggromito@arup.com
Valérie Hayez
Principal Scientist
Dow
valerie.hayez@dow.com
Keywords
Paper content
Introduction
Aesthetic desires to provide transparency in podium levels of buildings increase the potential use of glass in its construction. These lower levels of a building are most vulnerable for
Access Restricted
Rights and Permissions
[1] Silicone structural glazing under blast loading, Valérie Hayez, Jon Kimberlain, Jie Feng, Sigurd Sitte, Mark Mirgon, Glass Struct. Eng, 2022
[2] Descamps, P., Durbecq, S., Hayez, V., Chabih, M., Van Wassenhove, G.: Dimensioning silicone joints used in bomb blast resistant facade systems. In: Proceedings of Challenging Glass 6, Conference on architectural and structural applications of glass, Belis Bos & Louter, Ghent University (2018)
[3] Aggromito, D., Tartasky, M., Wholey, W., Farley, J., Klimenko, J., Pascoe, L.: Modelling laminated glass in LS-DYNA under extreme loading conditions. In: 13th European LS-Dyna Conference, Ulm Germany (2021)
[4] Aggromito, D., Pascoe, L., Klimenko, J., Farley, J., Tatarsky, M., Wholey, W. 2022, Simulation of PVB-glass adhesion and its influence on the blast protection properties of laminated safety glass. International Journal of Impact Engineering, Vol. 170
[5] Hooper P. PhD Thesis. Imperial College London; 2011.