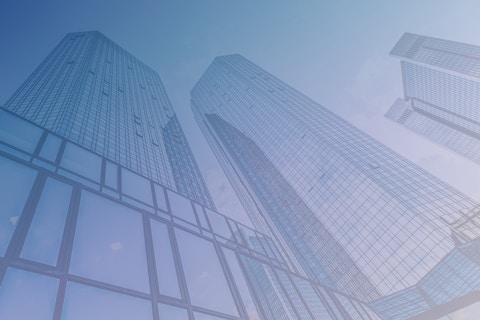
Explore the history of FTI events, including speaker and program details, presentation files, media, and other available assets.
Our upcoming FTI Student Forum explores the intersection of Facades, Carbon, and Circularity. In a fast paced spitfire format, architecture students present their recent work and research.
Our upcoming FTI Student Forum explores the intersection of Facades, Carbon, and Circularity. In a fast paced spitfire format, architecture students present their recent work and research.
Our upcoming FTI Student Forum explores the intersection of Facades, Carbon, and Circularity. In a fast paced spitfire format, architecture students present their recent work and research.
Our upcoming FTI Student Forum explores the intersection of Facades, Carbon, and Circularity. In a fast paced spitfire format, architecture students present their recent work and research.
The forum explores building development in Los Angeles in the Post-Pandemic Era and the Global Facade Market. The event is free but registration is required. See you there!
Presentations of outstanding projects in the LA area. More details will be announced soon. Make sure you're signed up to receive event updates. The event is free but registration is required. See you there!
More details will be announced soon. Make sure you're signed up to receive event updates.
The Facade Tectonics Institute's biennial World Congress, hosted October 12-13, 2022 in Los Angeles, gathers the built environment’s most influential players to discuss advancements revolutionizing the design and delivery of the building skin.
The topic of the Forum is Carbon Crisis: Leveraging the Façade System for Carbon Reduction in Buildings
The gap between simulated and actual energy performance has hobbled progress towards important carbon reduction goals in buildings and urban habitat. This summit advocates the need for improved energy modeling and the development of best practices, with emphasis on the building façade.
The virtual event series featured a panel among industry experts followed by a networking happy hour on the last two Fridays in March 2021.
FTI's half-day NYC Forum will take place virtually on Thursday, November 5, 2020, hosted by the Ornamental Metal Institute of New York. Join us for this year’s virtual event themed Pandemic Pantry: Digesting Covid-19 and Understanding the Lessons for Building and Facade Systems..
This year's World Congress was presented online through a virtual platform providing a unique forum for a diverse cross section of the design and real estate communities to discuss the innovations and advancements revolutionizing the design and delivery of the building skin.
.FTI's 2019 NYC Forum was an intimate, provocative and forward-looking dialogue with thought leaders from all sectors of the building industry; owners, architects, consultants, contractors and more.
FTI's celebrated Forum in Houston brought together thought leaders to explore the amplified threats of climate change in the unique urban context of Houston.
FTI's celebrated Forum in Seattle explored the "facade effect" on buildings and urban habitat with industry and academic thought leaders.
The sold out 2019 Toronto Forum brought together AECO industry thought leaders to confront themes central to ever-evolving facade technology, themes engaging facade design, delivery, renewal, materiality, sustainability and resilience.
FTI touched down in Minneapolis to confront themes central to the ever-evolving facade: energy-efficiency and sustainability, digital technology, kinetic and dynamic components, and material evolution.
FTI held its celebrated Forum in Miami with thought leaders to explore the amplified threats of climate change in the unique urban context of Miami.
Search by...